Parliamo del ruolo del coke nel processo di altoforno. Diamo un'occhiata più da vicino all'essenza di questa produzione metallurgica.
Oggi, il ferro e l'acciaio sono realizzati utilizzando il processo di altoforno, in cui il forno è un componente importante.
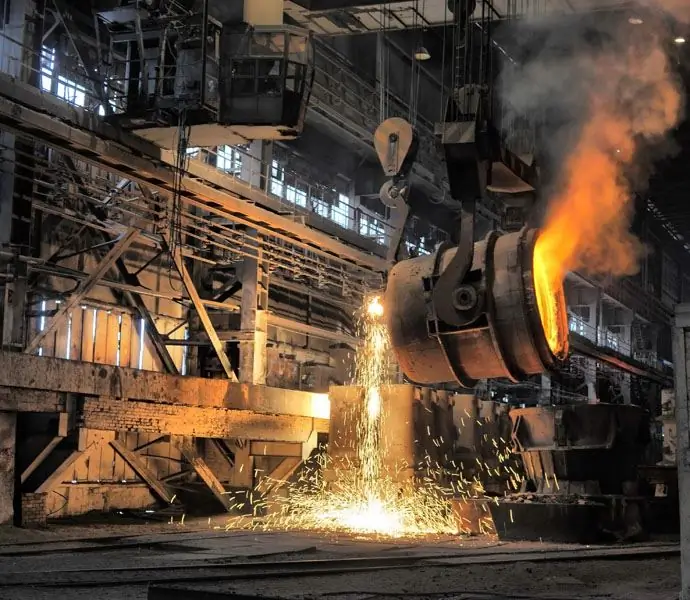
Specifiche dell'unità
Considera le caratteristiche del dispositivo, il suo scopo. I principali processi dell' altoforno sono associati alla fusione del coke. È un materiale poroso che viene sinterizzato da una massa di carbonio ottenuta calcinando il carbone senza la presenza di ossigeno atmosferico.
Un altoforno è un'unità potente e ad alte prestazioni, in cui viene consumata una quantità significativa di scoppio e carica.
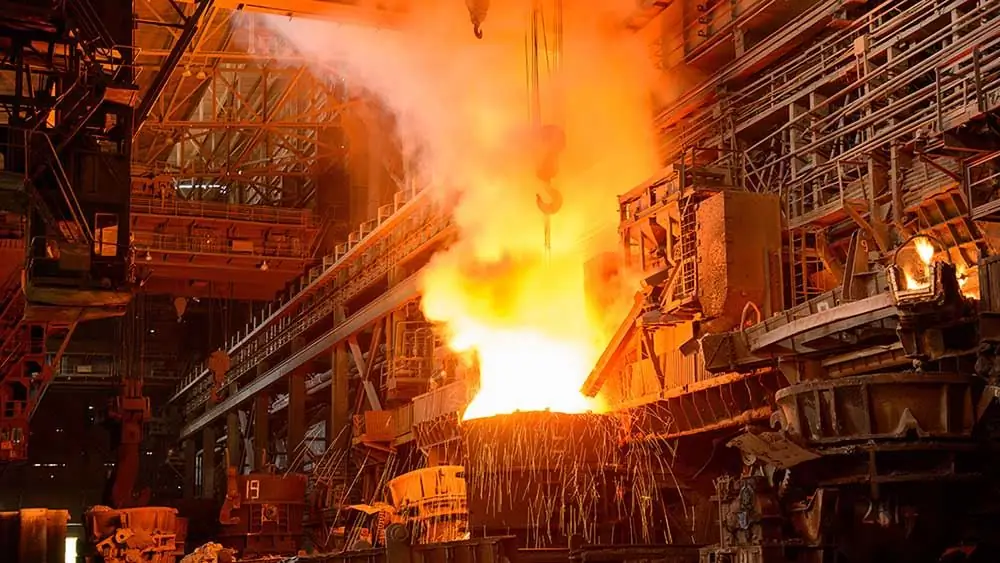
Caricare materie prime
L' altoforno moderno richiede che i materiali rimangano al suo interno per 4-6 ore, le sostanze gassose - 3-12 secondi. Se i gas sono completamente distribuiti sulla sezione trasversaleforni, potete contare su alti tassi di fusione, la produzione del ferro è in corso. Il processo di altoforno prevede la presa in considerazione del movimento dei gas attraverso zone che hanno una resistenza di carica inferiore. Pertanto, quando viene caricato nel forno, viene eseguita la regolazione, la ridistribuzione del coke e della sinterizzazione sulla sezione trasversale del forno in modo che differiscano per la permeabilità ai gas. In caso contrario, una maggiore percentuale di gas lascerà il forno con una temperatura significativa, il che influenzerà negativamente l'uso dell'energia termica, il processo di altoforno non sarà completamente efficiente.
In quelle aree ad alta resistenza, la miscela di gas passerà leggermente riscaldata, sarà richiesto ulteriore calore nella parte inferiore del forno, di conseguenza, il consumo di materie prime aumenterà notevolmente.
Quali altre funzionalità sono importanti da considerare durante il download? Il processo di altoforno per la produzione della ghisa è una produzione ad alta intensità energetica. Ecco perché uno strato di agglomerato meno permeabile ai gas viene utilizzato vicino alle pareti del forno e uno strato di coke viene aumentato al centro, grazie al quale il flusso di gas viene ridistribuito al centro. I materiali sono distribuiti uniformemente lungo la circonferenza.
La carica viene caricata in porzioni separate - feed. Una porzione è composta da diversi cassonetti, parte minerale (agglomerato), coca cola. Il rapporto tra gli ingredienti originali è determinato dagli esperti.
Il processo di altoforno consente la co-alimentazione delle materie prime, in cui le botti di coke e di sinterizzazione vengono raccolte su un grande cono e quindi caricate in un forno.
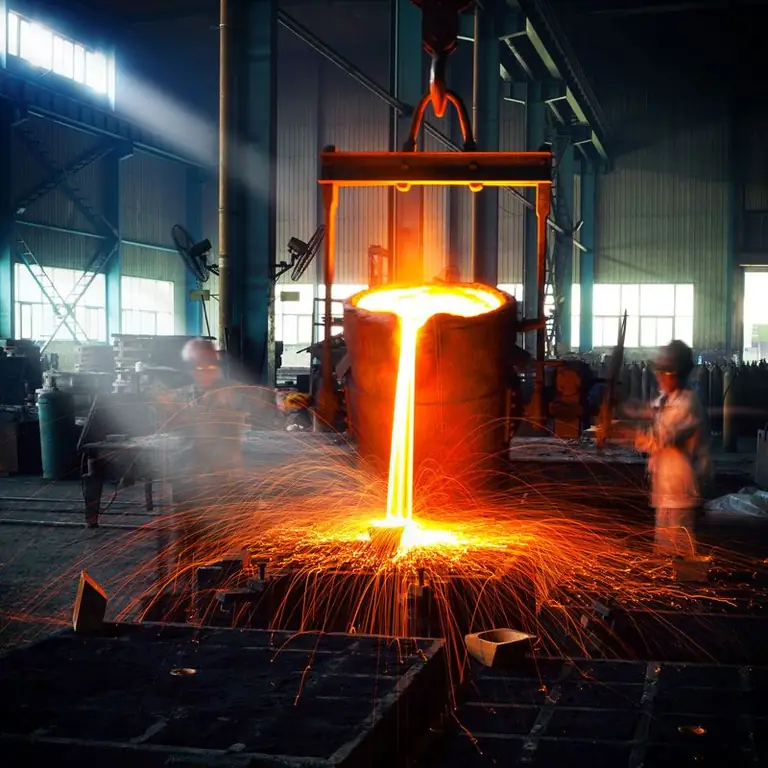
Adeguamento distribuzione batch
La distribuzione di coke e agglomerato sulla sezione trasversale delle sommità è controllata con i seguenti metodi:
- cambiare l'ordine delle materie prime sul cono grande;
- Si applicano servizi divisi e divisi;
- piastre mobili sono installate vicino alle pareti del piano.
Il processo di altoforno prevede la presa in considerazione di alcune regolarità per l'introduzione di materiali sfusi:
- posa di materie prime che cadono da un grande cono su un piano rialzato - un pettine;
- Alla cresta (nel punto di caduta) della carica si accumulano le multe, grossi pezzi rotolano fino ai piedi della cresta, quindi, in questa zona, la permeabilità ai gas della carica è maggiore;
- la cresta è influenzata dal livello di riempimento in alto, così come dalla distanza con un grande cono;
- il grande cono non scende completamente, quindi piccoli pezzi di coca cola arrivano alla periferia.
La maggior parte del centro del forno riceve il materiale dai cassoni di alimentazione, che sono stati gli ultimi ad essere caricati nel grande cono. Se modifichi l'ordine di caricamento, puoi ottenere una ridistribuzione dei materiali attraverso la sezione trasversale della parte superiore.
Per controllare il processo di distribuzione della carica utilizzata sul volume del forno, vengono utilizzati due apparati a cono. Recentemente alcuni altiforni sono dotati di piastre mobili in prossimità delle pareti del piano, che consentono di modificare l'angolo di inclinazione, spostandole lungo un piano orizzontale.
Pezzi della carica che cadono sui piatti vengono riflessi da essi, il che consente di dirigere la materia prima in determinate zone del piano.
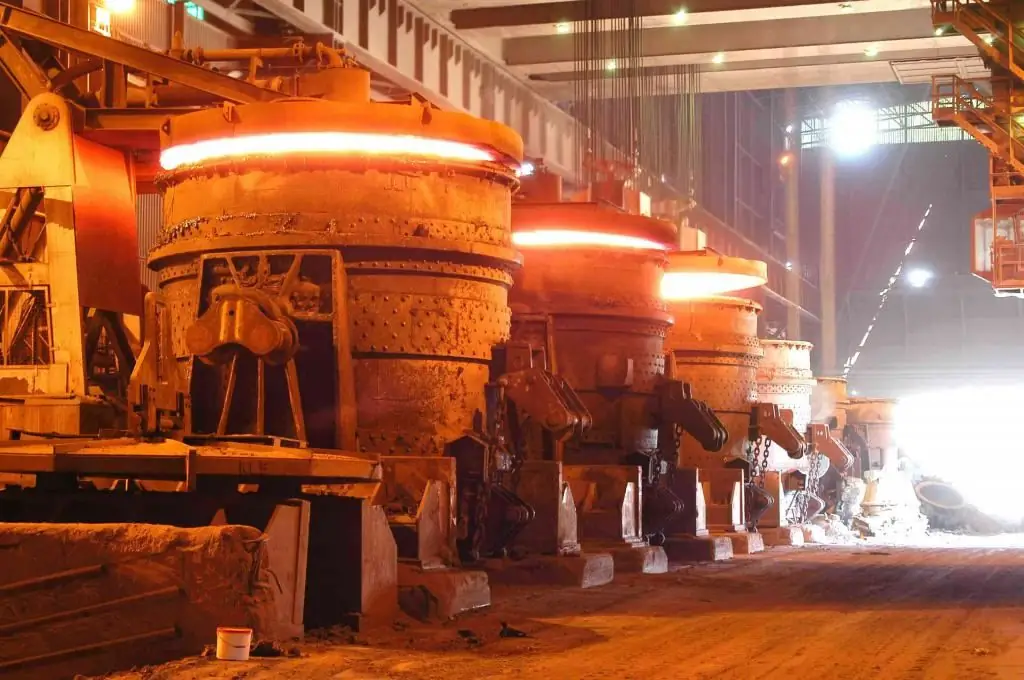
Opzioni stufanessuna conicità
Nei forni sprovvisti di dispositivo di caricamento a cono, il carico delle materie prime avviene tramite due tramogge di chiusura ad apertura alternata. Le materie prime vengono consegnate loro da nastri trasportatori inclinati, sui quali si trovano coke e sinterizzazione a intervalli chiari. Una porzione viene dal nastro in un bunker, quindi viene scaricata sulla sommità del forno lungo un vassoio inclinato rotante. Durante il periodo di scarico compiono una decina di giri completi attorno all'asse centrale fisso.
Ciclo di carico
È consuetudine chiamarlo un numero ripetuto di lotti di materiali caricati. La porzione massima è determinata dal volume della tramoggia di blocco del meccanismo di ricarica. Il numero di porzioni in un ciclo può variare da 5 a 14. Come ottenere integralmente i prodotti dell' altoforno? Per rispondere a questa domanda, diamo un'occhiata più da vicino all'essenza del processo. Con un maggiore contenuto di anidride carbonica nella miscela, la bassa temperatura contribuisce alla completezza dello scambio termico e dei processi chimici nell' altoforno. Affinché l'apparato funzioni in modo economico e intensivo, è necessario ridurre il contenuto quantitativo di anidride carbonica lungo l'asse e alla periferia del forno e aumentare ad un' altezza di uno o due metri dalle pareti.
Il controllo della temperatura nei forni nuovi viene effettuato introducendo le sonde attraverso i fori della cassa. Obbligatorio per tutti i processi è il controllo del livello di riempimento in alto.
Tra le innovazioni c'è l'uso di metodi di misurazione del livello senza contatto basati sulle letture di sensori a microonde e infrarossi.
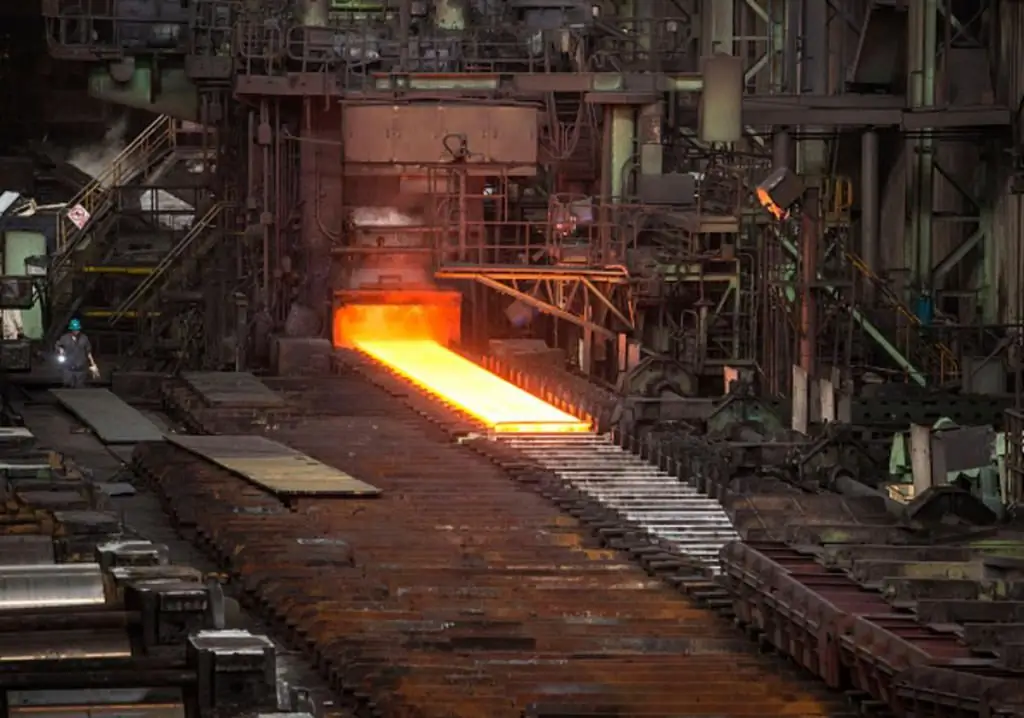
Caratteristiche di distribuzione della temperatura
Oltre al calore che viene introdotto dal getto termico, quale principale fonte di calore per il riscaldamento dei gas e della carica, svolgendo il recupero e compensando le dispersioni di calore, è possibile compensare le perdite con il calore che viene ceduto durante la combustione del combustibile nella parte superiore del focolare. Quando i prodotti gassosi si muovono verso l' alto dal focolare, il calore scende ai materiali freddi in carica e si verifica lo scambio di calore. Un processo simile spiega la caduta di temperatura da 1400 a 200 gradi all'uscita della parte superiore del forno.
Rimuovere l'umidità in eccesso
Consideriamo i principali processi fisici e chimici in un altoforno. Nella carica, che viene caricata nell' altoforno, è presente umidità igroscopica. Ad esempio, nella composizione della coca cola, il suo contenuto può arrivare fino al cinque percento. L'umidità evapora rapidamente sulla parte superiore, quindi è necessario ulteriore calore per rimuoverla.
L'umidità appare quando il minerale di ferro marrone e il caolino vengono caricati nell' altoforno. Per risolvere il problema nella moderna produzione di ferro, questi minerali non vengono praticamente utilizzati come materie prime.
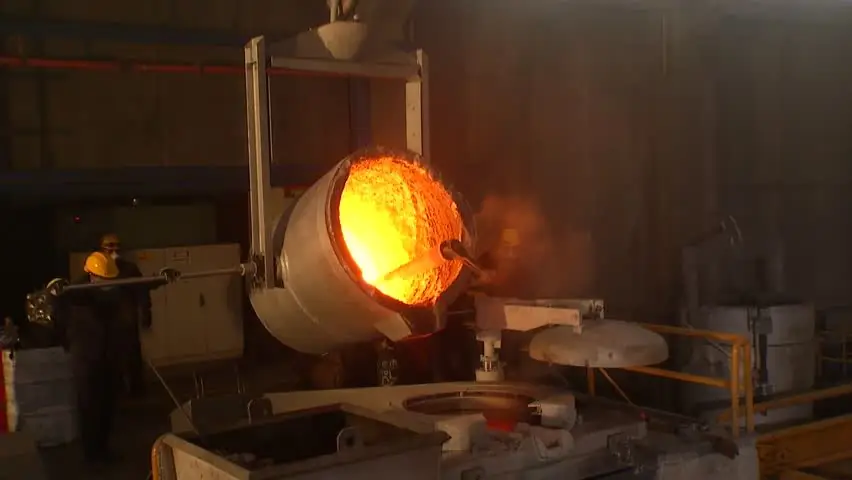
Processi di decomposizione dei carbonati
I sali dell'acido carbonico possono entrare nell' altoforno. Man mano che si riscaldano, si decompongono in ossidi di calcio e carbonio e il processo è accompagnato dal rilascio di una quantità sufficiente di energia.
Di recente, quasi nessun minerale è stato caricato negli altiforni. Qual è il ruolo dei flussi nel processo di altoforno? Aumentano la sua efficaciaconsentono di ridurre i costi di produzione. Grazie all'utilizzo della sinterizzazione flussata, la completa rimozione del calcare dalla carica dell' altoforno può ottenere un notevole risparmio di coke. Il processo di decomposizione del calcare durante l'agglomerazione è fornito dalla combustione di combustibile di bassa qualità.
Recupero del ferro
Il ferro viene introdotto nell' altoforno sotto forma di ossidi. L'obiettivo principale del processo è massimizzare l'estrazione del ferro dagli ossidi mediante riduzione. L'essenza del processo è rimuovere ossigeno, carbonio, monossido di carbonio, idrogeno sono usati per questo. La riduzione con il carbonio è chiamata processo diretto e la reazione con sostanze gassose è chiamata interazione indiretta. Quali sono le loro caratteristiche distintive? Nella reazione diretta viene consumato carbonio, per cui la sua quantità viene significativamente ridotta. Il secondo tipo di riduzione del ferro dagli ossidi richiede una quantità eccessiva di idrogeno.
Il processo produce ferro solido. Il grado di recupero della ghisa è del 99,8%. Pertanto, solo lo 0,2 -1% si trasforma in scorie.
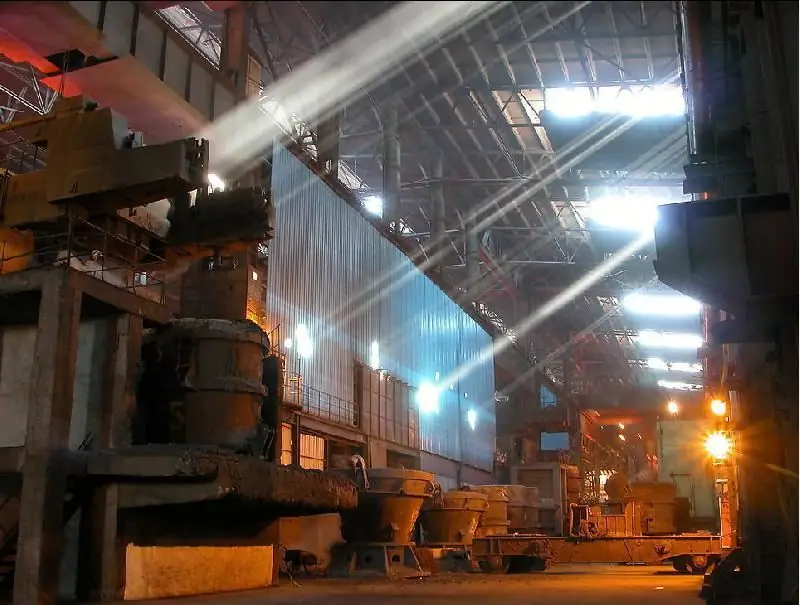
Fusione della ghisa al manganese
Nel processo di fusione della ghisa rigenerata, il manganese entra nell' altoforno sotto forma di agglomerato. In alcune quantità, i minerali di manganese sotto forma di silicati di manganese contribuiscono alla produzione di ghisa al manganese.
Il recupero dagli ossidi di manganese avviene per gradi. Per completare il processo, è necessario impostare temperature elevate nel forno. Il processo di fusione della ghisa è accompagnato dariduzione del manganese solo nel rapporto del 55-65%. Attualmente, a causa della scarsità di minerali di manganese e manganese, nella catena tecnologica è stata utilizzata una piccola quantità di ghisa al manganese. Quando si passa alle ghise a basso contenuto di manganese, è possibile risparmiare non solo il manganese stesso, ma anche il coke, poiché il suo consumo per la riduzione diretta del metallo diminuirà.
Conclusione
Il processo di altoforno è uno dei principali metodi di fusione del ferro e dell'acciaio. A seconda di quali componenti vengono introdotti nella miscela iniziale, si ottengono attualmente varie tipologie di prodotto finito. Tra i settori di applicazione della ghisa e dell'acciaio risultanti, segnaliamo: ingegneria meccanica, industria chimica, medicina, costruzione di strumenti.